#170459 - 04/21/18 10:44 AM
Re: The Big Tough Folder...
[Re: desert.snake]
|
Knife Enthusiast
Registered: 02/06/16
Posts: 656
|
Yes, any test should test blade against material, not test blade against test equipment. A good blade will have a hard edge and be progressively springy and soft towards the back, which is why no wood carver uses steel hammers on his carving tools. Blade backs and handles are not steel tool beating surfaces, and a wood or leather mallet is needed. Rubber bounces and robs blow of force. The demarcation line of harder/softer can be seen as a shadow on this forged blade. 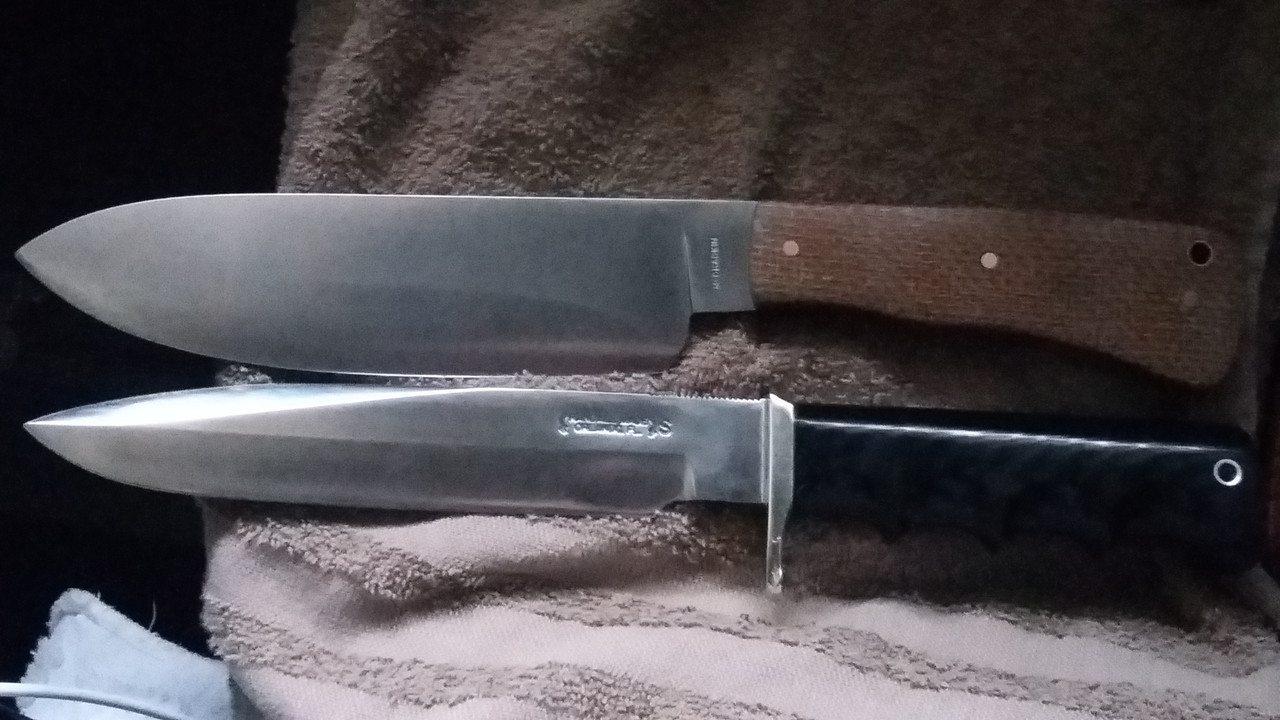
_________________________
Cadent a latere tuo mille, et decem millia a dextris tuis; ad te autem non appropinquabit.
|
Top
|
|
|
|
#170461 - 04/21/18 12:54 PM
Re: The Big Tough Folder...
[Re: Lofty]
|
Knife Enthusiast
Registered: 09/25/13
Posts: 1189
Loc: the other side of the earth
|
Absolute classics! It seems I saw him (the upper knife) on cuttingedge, right? Previously used composite technology, this is not zone hardening, it's better, since we know exactly where high-carbon steel  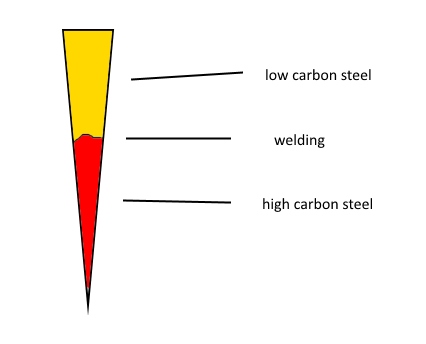
_________________________
Si vis pacem, para bellum
|
Top
|
|
|
|
#170464 - 04/21/18 01:25 PM
Re: The Big Tough Folder...
[Re: desert.snake]
|
Knife Enthusiast
Registered: 02/06/16
Posts: 656
|
Slowly but surely getting off the folder topic, and next will be Glocks, but...why not? I have two identical knives made by VJ, or had, gave one to a friend. VJ (who has had his MS stamp for a quarter of a century) uses that design muchly, his working grade knives, forged leaf spring steel. Here is a video of him roughing out a similar blade, and he puts a lot of work into his knives, including the tapered tang which is forged and not ground. The burlap "micarta" he made, as well. Continue watching until complete end of video and still photos pop up showing various stages, leaf spring to finished blade. Note most every blade/handle detail is done at the forge. https://www.youtube.com/watch?v=CJ7I72mmMJ4If I had to depend on one knife, this would be it. A straight razor, log splitter, meat cleaver, all around kitchen knife. One of my most favorite users, tried to angle to hide scratches to highlight knife, somewhat successfully. The handle has a neat 3-D look to weave, even though smooth as a baby's behind. I would pay Rick Hinderer whatever he wanted, to have such a blade on a folder. It is no coincidence the blades are so similar. Including the Model 16. 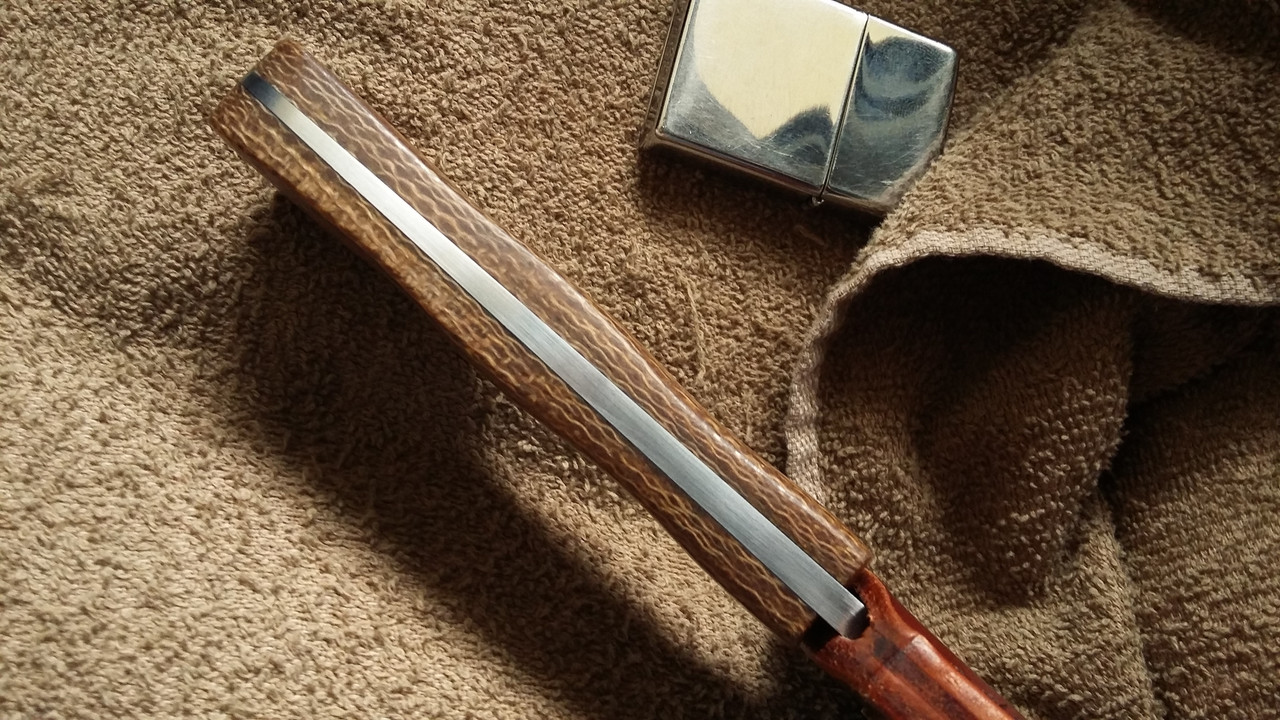 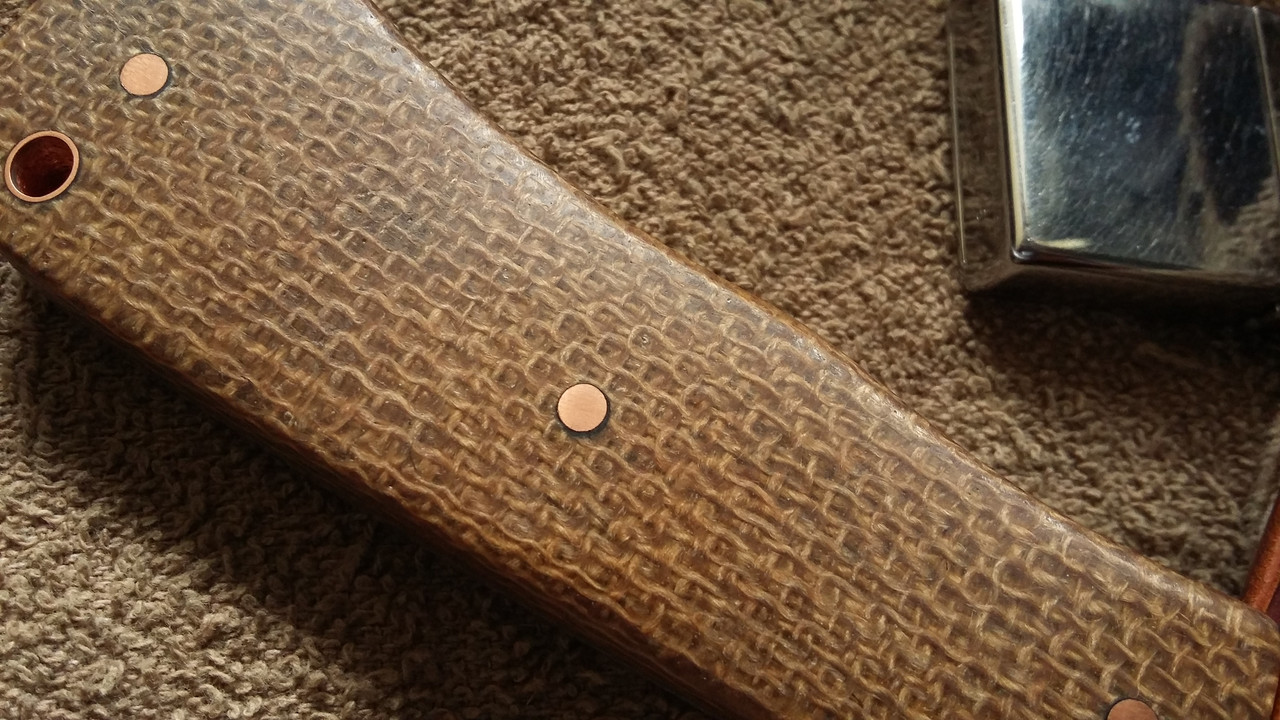 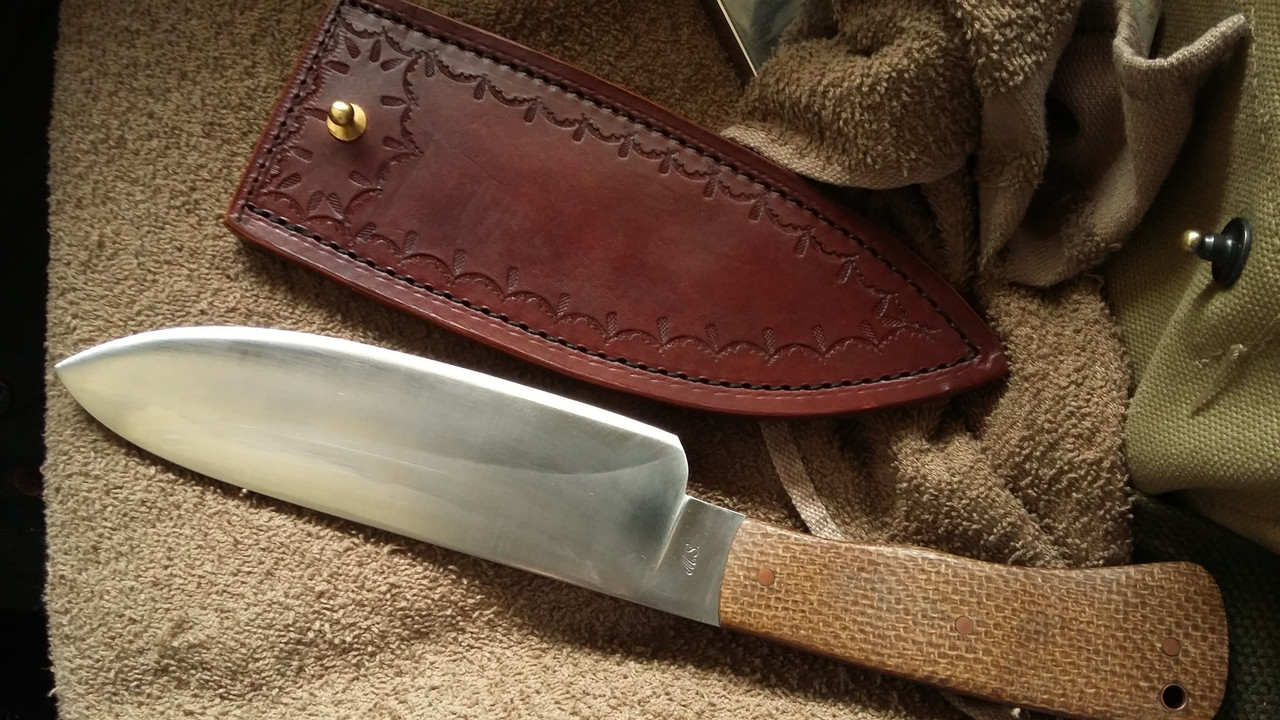 As for welding harder/softer in places, it has been around since Celts and 400BC and pattern welding twist rod with inserts, Vikings learned the craft likely from them and perhaps even kidnapped slave smiths. The actually higher carbon can still chip, so, no knife is perfect...My vote always goes for tough first, as broken edge or blade is no good to anybody for anything. I would truthfully prefer both Hinderer and Reeve used far tougher 3V, but all the collectors would cry the knives required care and still rusted in spots, and these guys flick their knives somewhere between 1.5 million and 20 million times a day. They also complain when they wear out. AND...really need to get back on folders, this being the folder forum and all.
Edited by Lofty (04/21/18 02:15 PM)
_________________________
Cadent a latere tuo mille, et decem millia a dextris tuis; ad te autem non appropinquabit.
|
Top
|
|
|
|
#170466 - 04/21/18 02:37 PM
Re: The Big Tough Folder...
[Re: Lofty]
|
Knife Enthusiast
Registered: 02/06/16
Posts: 656
|
Edited by Lofty (04/23/18 12:54 PM)
_________________________
Cadent a latere tuo mille, et decem millia a dextris tuis; ad te autem non appropinquabit.
|
Top
|
|
|
|
#170469 - 04/21/18 03:34 PM
Re: The Big Tough Folder...
[Re: Lofty]
|
Knife Enthusiast
Registered: 09/25/13
Posts: 1189
Loc: the other side of the earth
|
Daniel Winkler makes folding knives, I've been looking at them for a long time, but have not bought yet. I do not know he forged it or not, but there is quality hardening there (if it is the same processing as for its fixed blades). This is a photo from his site. They quickly lose their virginal appearance if they are used.
Attachments
------
_________________________
Si vis pacem, para bellum
|
Top
|
|
|
|
#170470 - 04/21/18 03:40 PM
Re: The Big Tough Folder...
[Re: desert.snake]
|
Knife Enthusiast
Registered: 02/06/16
Posts: 656
|
Dan was forging, has MS rating, still does some custom work, but decided demand was enough that he could offer ground barstock lines, and his factory blades are excellent tough for hard use. I had not seen a folder before, and so, have no comments as to his design as for strength or durability. Knowing him, it SHOULD be quite good.
_________________________
Cadent a latere tuo mille, et decem millia a dextris tuis; ad te autem non appropinquabit.
|
Top
|
|
|
|
#170471 - 04/21/18 03:43 PM
Re: The Big Tough Folder...
[Re: Lofty]
|
Knife Enthusiast
Registered: 02/06/16
Posts: 656
|
Looked more into Winkler's operation, and saw hints of a new more tacticool appearing folder on the horizon, but not sure if a solid intro.
Also looked into his steels, it seems initially his stuff was 52100 (which I call great for a skinner, but not so great for shock), then he moved to more suitable 5160, and then went up a notch on that to 80CRV2, both the latter two great for tough as nails, the last one toughest of all.
Edited by Lofty (04/22/18 02:22 PM)
_________________________
Cadent a latere tuo mille, et decem millia a dextris tuis; ad te autem non appropinquabit.
|
Top
|
|
|
|
#170692 - 04/29/18 10:09 PM
Re: The Big Tough Folder...
[Re: Lofty]
|
Knife Enthusiast
Registered: 02/06/16
Posts: 656
|
As for folders not quite as big, but tougher than most larger, the Hinderer XM line runs 3"/0.145" thick (a scale model by request of the cubical/office crowd styling today with oxymoronical "tactical EDCs" and who likely carry 3" "fighters", too), 3.5"/0.165" (original size hot number with military/firefighters), and 4"/0.185" (requested by gloved military/first responders, Rambo, and myself, of course). Most large folders of Endura size run circa 1/8th"/0.125. For even tougher than previous posted spearpoint knife, Rick originally did his hallmark cross between a tanto and spearpoint, called whimsically, Spanto, which still is immensely popular. It features the exact same blade silhouette as the spearpoint (visa versa, actually). The difference being not as acute primary grind leading to an even thicker edge, and even less acute on the flat front grind, to an even thicker edge than that of the belly. On a 3/16ths" thick blade already quite stout. Still quite useful an edge, and finer than most 3/16ths" modern tough fixed blades, but the spearpoint certainly better for finer cutting angles. I admire a fireman/military tough knife able to dismember seats and dashboards or rip a hole through a door to unlock other side, bust airdrop pallet straps, still remain a knife, and in a folder, no less. Small wonder guys in services snap these up. Rick has been one of the few to not gouge during peak demand, and, instead, used his going from handmade to shop made to increase quality/precision, to where he was making much of his profit increase on the bottom end via cost cutting such as tool life increases vs raising prices. When his XM-18 3.5" came out circa 2006 it was a $385 knife. Today, it is $425...the $385 bumped quickly to $390, sat there for years, even as his knives sold third party for $800-$1000. As the bubble burst, as eventually they all do, nobody took a hit who bought direct. It was bad enough at the time that fire and police agencies lucky enough to have budget to supply such gear, were having fire stations buy and then flip their knives for a profit, abusing Rick's preferential treatment of our finest. It was sad. Strangely, he still only makes several thousand per year in his 15 man shop, by batches, and freely admits most of company income still from design royalties from major factories. 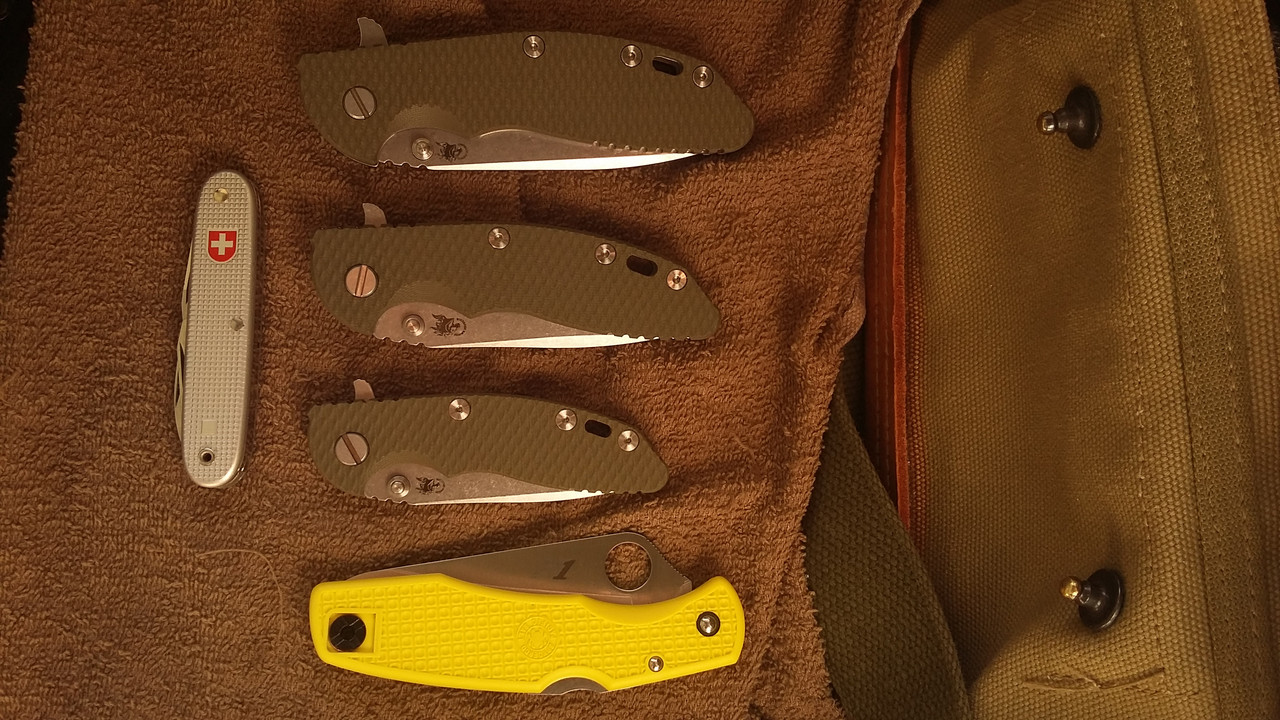 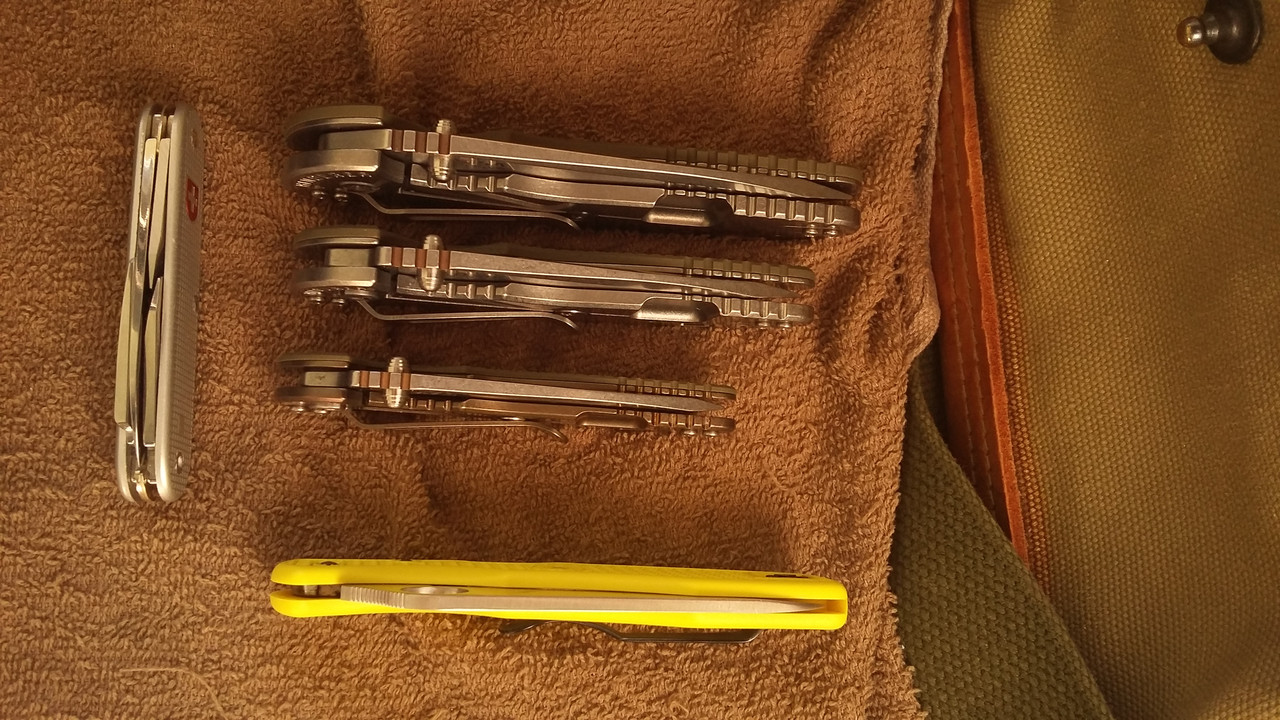 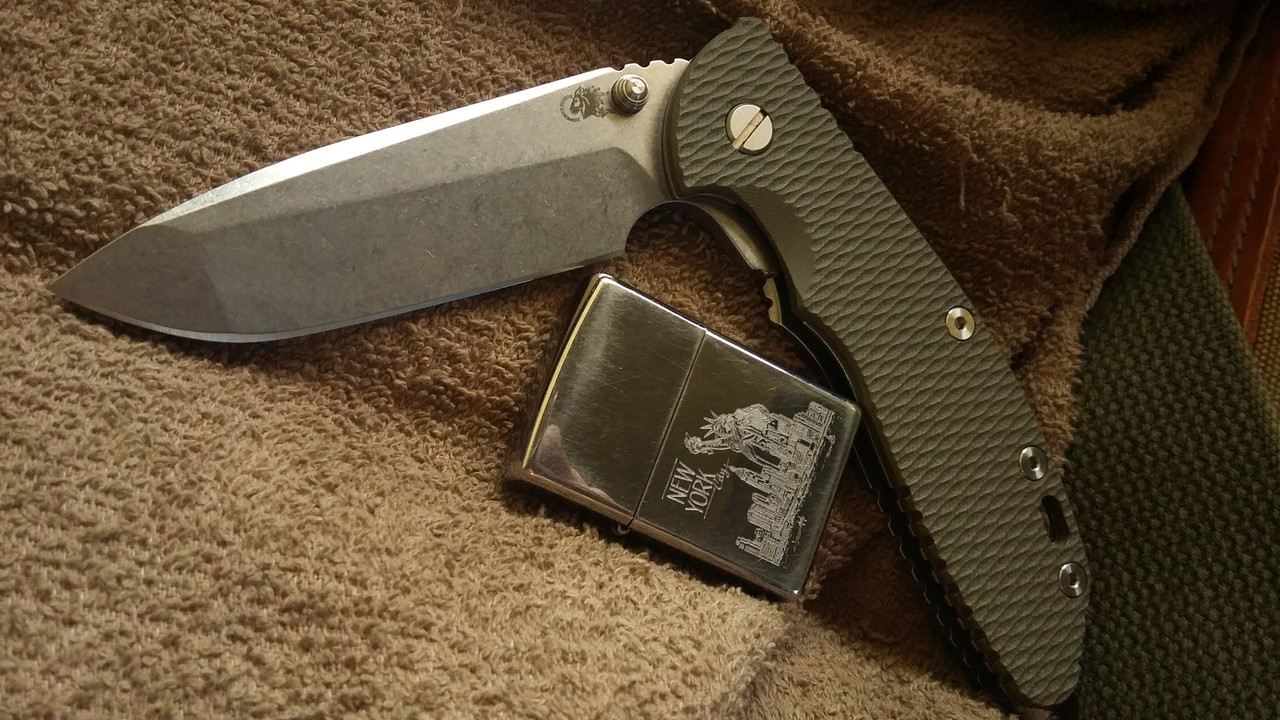 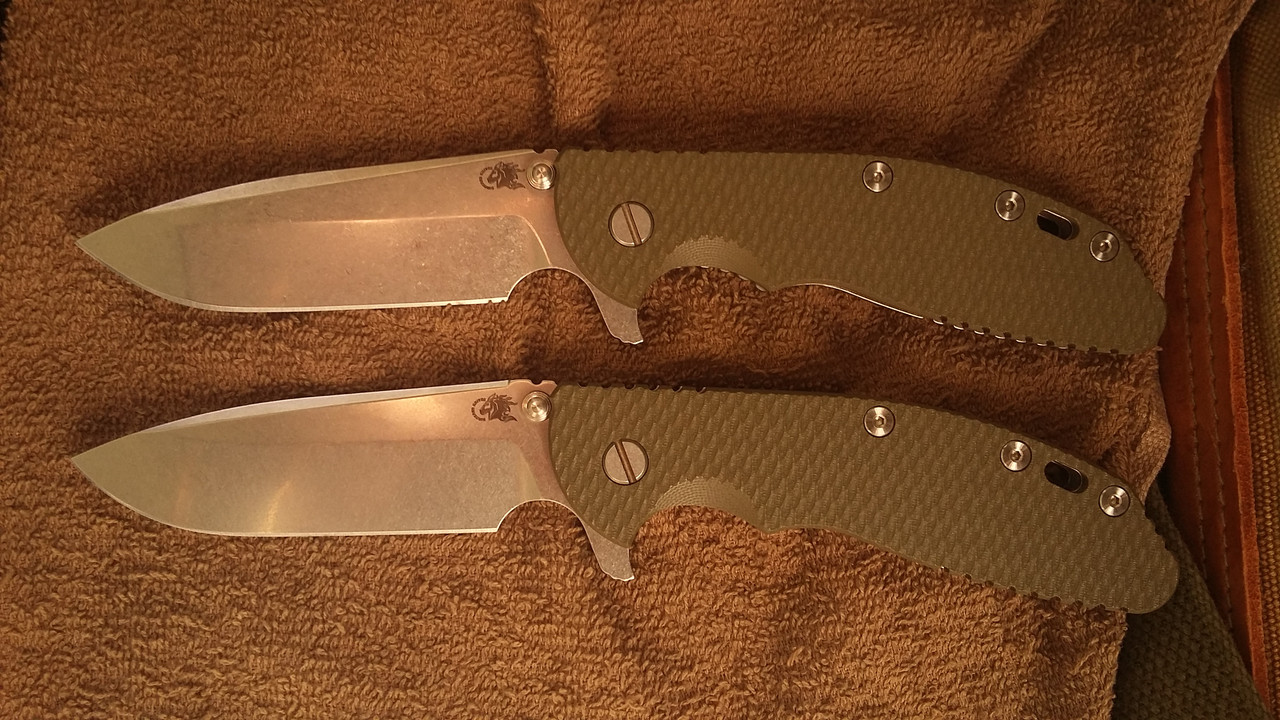 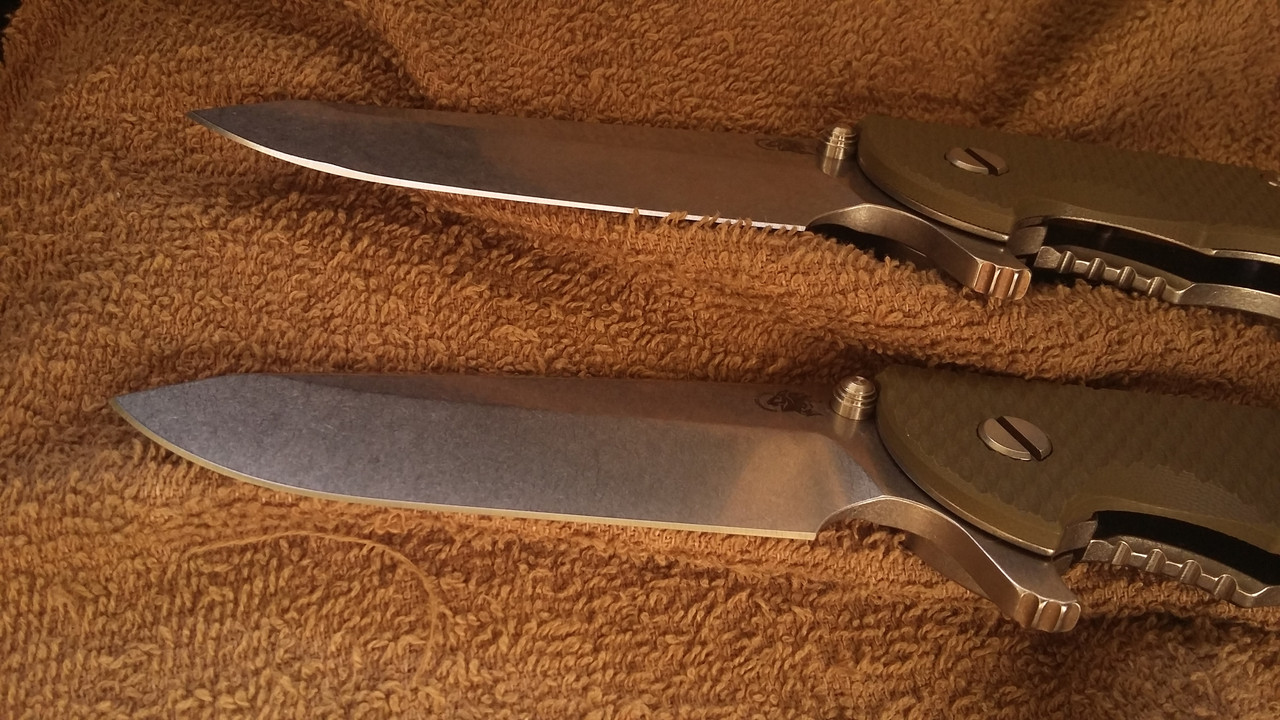 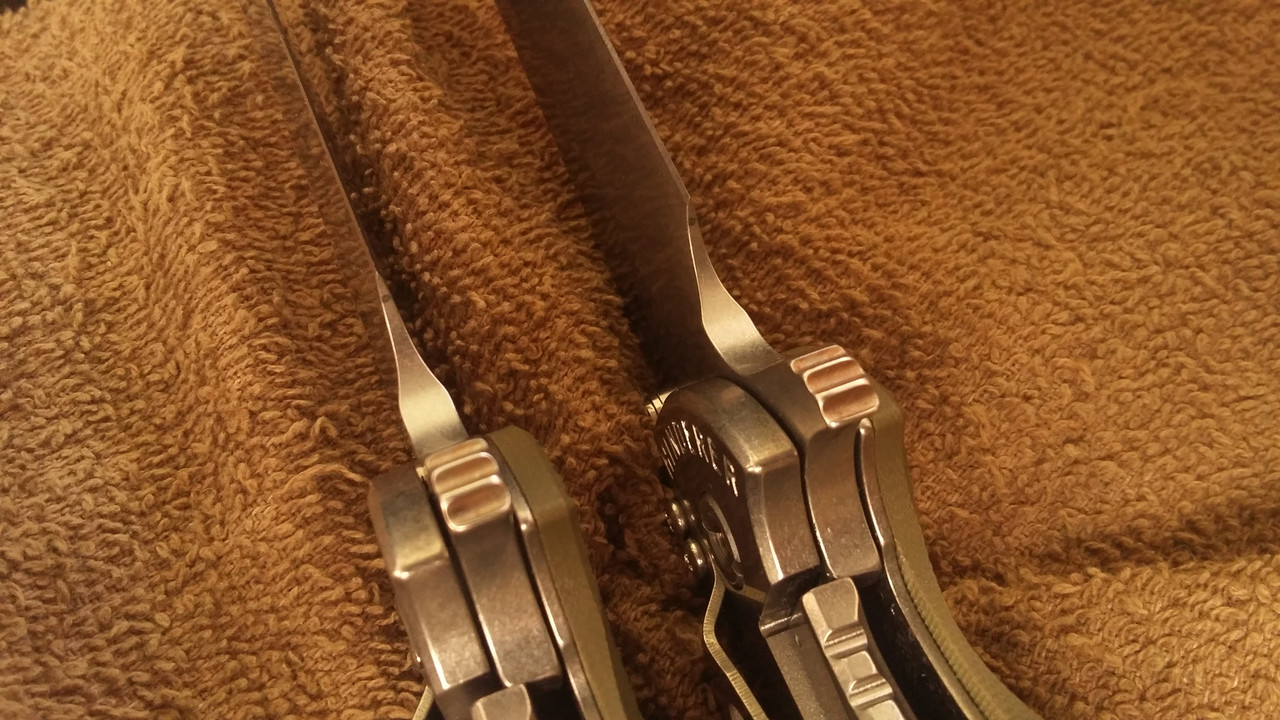 the "dark" spots on choils are actually shiny contact points from stop pin when folded. PS-after posting these, I noticed both pivot screws on the larger pair clocked to same setting. Rick is all about precision to 1/2 thousandth inch, all work and parts done in-house aside from blade primary bevels/heat treat and clip screws, his tolerances of aerospace quality, as is gauging using latest computerized optical comparators for hole location, critical surface locations, and runout. But the clocking had to have been a fluke, as I have dis/reassembled these knives, adjusted tension to my own likes to where both felt the same, and this had to have been a fluke, for sure, right?
Edited by Lofty (04/30/18 06:10 PM)
_________________________
Cadent a latere tuo mille, et decem millia a dextris tuis; ad te autem non appropinquabit.
|
Top
|
|
|
|
#170722 - 04/30/18 03:10 PM
Re: The Big Tough Folder...
[Re: Lofty]
|
Knife Enthusiast
Registered: 09/25/13
Posts: 1189
Loc: the other side of the earth
|
Randomness does not exist. Many thanks for such an interesting excursion into the history  Rick makes excellent knives, for my taste I would have made the hilt thicker
_________________________
Si vis pacem, para bellum
|
Top
|
|
|
|
#170727 - 04/30/18 03:36 PM
Re: The Big Tough Folder...
[Re: desert.snake]
|
Knife Enthusiast
Registered: 02/06/16
Posts: 656
|
It actually is randomness, as where I had the 1/4" pivot indexed on back side was strictly dictated by spanner fitting best in a certain orientation, with clip still in the way. A knife blade stock thicker than 3/16ths"/0.185"/4.7mm is going to be a monster, the jump from the 3.5"/0.165" thick knife to the 4"/0.185" thick blade also jumped weight from 5.7 oz to 7.8 oz. I would simply prefer a stronger tougher steel such as 5160/80crv2/8760m be used, to not increase already considerable folded size and thickness. To continue the history, the handmade 3.5" knife introduced 2006, shop made by 2008, the largest blade introduced 2008, still handground and all titanium, the shop made 2010 intro at BLADE with G10 (where I bought my first one via lottery, will post a photo when I dig it up), and the smallest knife introduced between the two. As for cost cutting, mainly through better machines and programming, his tool replacement way down while production is up, suchlike new equipment means no more buried and wrecked cutters. Rick is a self-taught machinist, no easy task. He went outside his shop for primary grind and heat treat of his blades, strictly to increase repetitive quality over hand ground, while also increasing ability to keep up with demand. They still will do a hand ground, but you are taking one guy of a small crew off a busy schedule, and you WILL pay for that...I never really looked into it, but might still be Rick doing those, and a man has to feed his original STG44 and Browning General Purpose Machinegun, you know? Personally, I like the outfit because although he has sold vast numbers of knives to elite military members, he does not cater to that, nor cater to snob/elitism at all in advertising, nor to gory imagining armchair commandos. No "Deathwind Skull Cleaver II", nor "Tools For The PROFFESIONAL Operator". Any hype has always been dealers, along with hyped prices. His motto is simply Dependable Custom Knives. Where others embellish with gargoyles, skulls, etc, Rick embellishes with dog paw prints, interlocked turning gears, and dinosaur skin texture. His emphasis is on precision workmanship, and here is a video concentrating mainly on the TWO people fitting blades, with one blanked out for privacy request. Most of the video fitting up ONE knife, if that is what it takes. https://www.youtube.com/watch?v=C0I482ZeqTwThis second video, and actually part 1 of the above series, is a tour of shop as various parts made. Again, they batch produce, so not everything being made all at one time, a very small outfit. Be warned of terrible audio, no award winning film making here. https://www.youtube.com/watch?v=c1wryqsWjrcI was amused by the latter (Pt1) video, as Rick was showing off his QC equipment, and saying blades could "be checked, every however many blades" sampling, while later, the actual machinist flatly stated (since production pace obviously allowed) that he checked "every one of them". Which means a worker who is exceeding QC measures, simply because he can. Note, also, earlier in the video, a machine is making glorified washers named "lock bar stabilizers" of Rick's invention, and the obviously in-use QC checking gauges next to the batch of such simple little parts. As an aside, one can find all manner of self-proclaimed "expert" rants, including regarding Hinderer products. Liner and frame locks are a tricky balancing act, and frankly a terrible idea for a "lock" which actually works more as a sear and trigger opened or closed. Folk complain detent not strong enough to "fire" the unsprung blade opening as if a catapult trigger, or blade can open when shaken. Or even slight off-center tips. All of these issues are secondary to safe and proper amount of LOCK tension and engagement. When lock tension increased, so is opening and closing drag of detent on blade, depth of engagement and sticking or premature wear. Meaning folk then loosen the pivot for the other crowd who wants to flip the knife with a fingernail. It is impossible to please them all. So, if you want ultimate centered, there is an adjustment proceedure widely posted. It is supposed to POSSIBLY be able to shake open and which movement cannot be duplicated in pocket or IWB. If you want it to "fire", and never in a million years shake open, then disassemble and increase lock tension and enjoy the excess wear, and if you want it to flick, do the opposite and relieve tension, and if it pops closed on fingers during use, it is all on you. Back to the XM series knife itself, it is getting old in the now ever changing knife world. Rick and crew have introduced a steel insert to lock bar end, primarily to deal with warranty claims from those who insist on batoning a knife design which works only via direct spring pressure of spring on blade to hold open, and which is going to bounce and batter the softer titanium every time with blows to spine, despite Rick's design being nearly unbreakable with any force applied any other direction. Personally, I hate the added complexity due to knife beaters, but....when you batch produce for a series, alot a certain number for warranty, and you get a surge from knife beaters or pathological flickers who NEVER stop flicking, it can really throw a wrench in the gears. And as for design getting old, Rick is amazed it still in production, and that is due to demand. He has continued to crank out new designs, better ergonomics, most designs being geared to his larger pool of buyers mainly of only indoor adventurers and wanting more pocketable knives. And yet, it is still his XM slowly gaining classic status and still the one selling out first at dealers. And Spanto. And green or black or tan. And I fully admit partial fault in that.
Edited by Lofty (04/30/18 06:52 PM)
_________________________
Cadent a latere tuo mille, et decem millia a dextris tuis; ad te autem non appropinquabit.
|
Top
|
|
|
|
|
|